Robotic Welding: Enhancing Precision and Efficiency
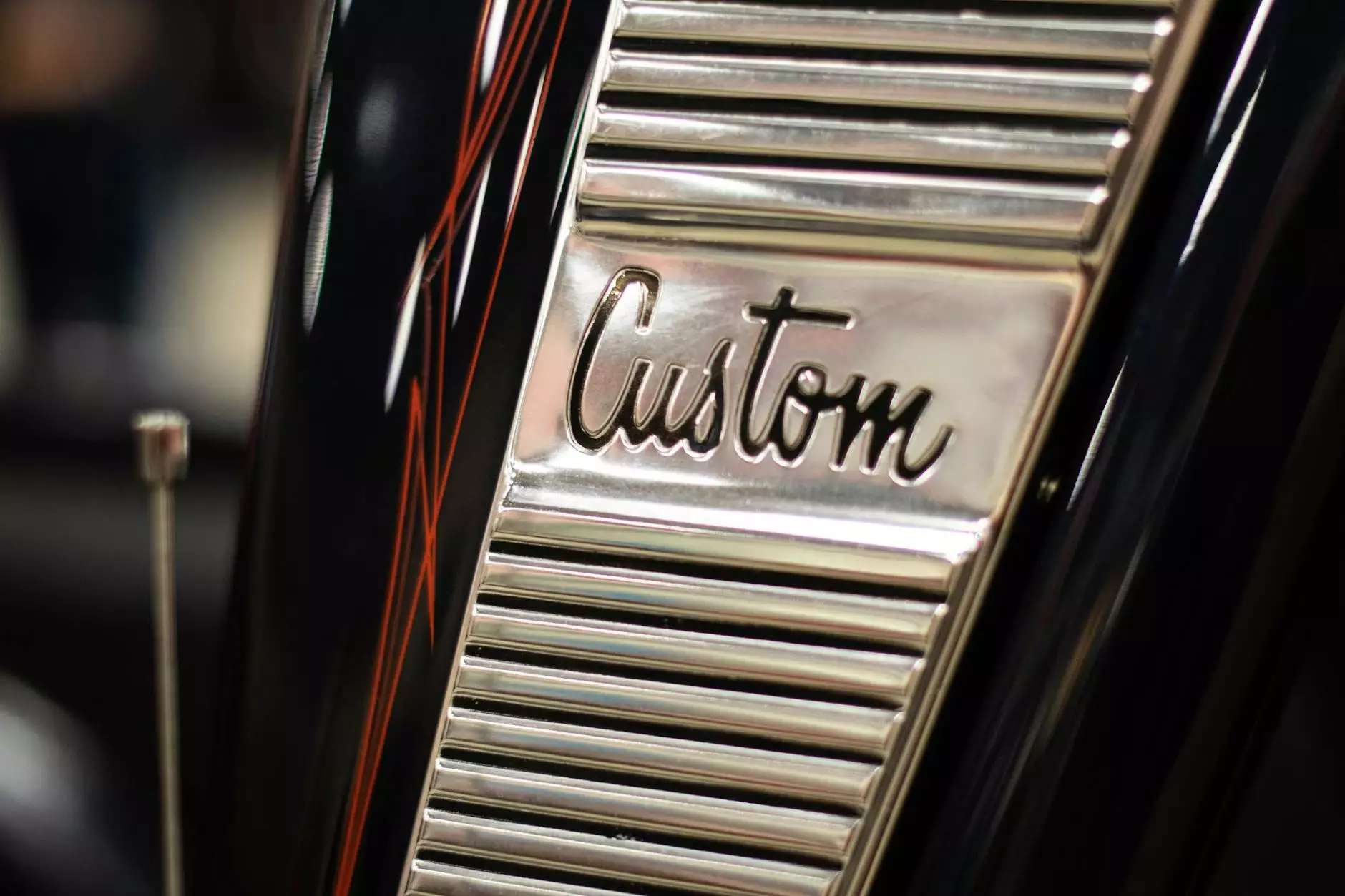
In the ever-evolving field of manufacturing and engineering, robotic welding has emerged as a game-changer, revolutionizing the way industries approach and execute the welding process. At Cresco Custom Metals, a reputable metal fabricator offering top-notch services in the Home & Garden, Furniture Stores, and Metal Fabricators categories, we employ state-of-the-art robotic welding technology to deliver precision and efficiency for our clients' projects.
The Specialized Language of Robotic Welding
Robotic welding involves a specialized language, rich in technical terms and concepts. This language forms the foundation for understanding and executing welding processes using robotic systems. It encompasses a wide range of terminology, including weld penetration, arc length, filler material, weld current, heat-affected zone, weld bead, and many more.
Understanding this language is essential for effectively operating robotic welding systems and achieving optimal results. It requires in-depth knowledge of various welding techniques, such as spot welding, seam welding, and gas metal arc welding (GMAW). By leveraging this language, professionals can communicate accurately and precisely, ensuring seamless integration of robotic systems into manufacturing and engineering processes.
Advanced Technology for Robotic Welding
Robotic welding at Cresco Custom Metals is powered by cutting-edge technology, encompassing robotic programming, sensor technology, and safety protocols specific to robotic welding. Our team of experts is well-versed in programming industrial robots to perform complex welding tasks with utmost precision.
Through the integration of sensors, our robotic welding systems can analyze real-time data, adjusting parameters such as arc length and weld current. This ensures consistent weld quality and optimal performance, even in dynamic manufacturing environments. Additionally, pioneering safety measures, such as protective barriers and light curtains, are employed to guarantee operator safety during the entire welding process.
Advantages of Robotic Welding
Robotic welding technology offers numerous advantages that make it an ideal choice for various manufacturing and engineering applications:
1. Enhanced Precision
Robots equipped with sophisticated algorithms and precise control systems can execute welds with exceptional accuracy, ensuring consistent weld quality throughout the production process. This level of precision minimizes rework, reduces material waste, and ultimately improves the overall efficiency of the welding operation.
2. Increased Efficiency
Robotic welding boasts impressive production rates, thanks to its ability to work continuously without fatigue. By programming robots to handle repetitive welding tasks, human labor can be redirected towards more intricate and specialized roles, optimizing workflow and achieving higher productivity.
3. Improved Safety
By reducing human involvement in hazardous welding processes, robotic welding significantly enhances operator safety. This technology eliminates the risk of occupational hazards, including exposure to noxious fumes, extreme heat, and potential accidents. At Cresco Custom Metals, we prioritize safety as a key aspect of our robotic welding solutions.
4. Cost-Effectiveness
Investing in robotic welding technology can yield substantial cost savings in the long run. The automation of welding processes eliminates the need for extensive manual labor, leading to reduced labor costs and increased efficiency. Moreover, robotic systems minimize material waste and contribute to consistent high-quality welds, which reduces rework expenses.
Applications of Robotic Welding
Robotic welding finds extensive applications across various industries. Some notable areas where the advantages of robotic welding truly shine include:
1. Automotive Industry
Robotic welding is widely utilized in the automotive sector for its ability to quickly and accurately weld vehicle frames, body components, and other structural elements. High-speed production lines and seamless weld quality contribute to the efficiency and reliability of automobile manufacturing processes.
2. Aerospace Industry
The aerospace industry demands utmost precision and reliability, making robotic welding an indispensable component of aircraft manufacturing. From welding intricate components to crafting robust fuel tanks, robotic systems ensure adherence to strict quality standards while maintaining efficiency in aerospace fabrication.
3. Heavy Machinery Manufacturing
With its capacity to handle heavy workloads and produce consistent welds, robotic welding is a boon for the heavy machinery manufacturing sector. From agricultural equipment to construction machinery, robotic welding systems ensure durability, structural integrity, and timely production.
4. Structural Steel Fabrication
Robotic welding enables efficient fabrication of structural steel components, such as beams, columns, and trusses. By automating the welding process, construction projects benefit from accelerated production rates, improved accuracy, and enhanced strength of steel structures.
These are just a few examples of the diverse applications of robotic welding. As technology advances, it is expected that this versatile welding method will find its way into even more industries, further optimizing manufacturing processes worldwide.
Partner with Cresco Custom Metals
When it comes to robotic welding services, Cresco Custom Metals stands as a trusted partner, delivering superior results for businesses in the Home & Garden, Furniture Stores, and Metal Fabricators sectors. Our team of skilled professionals and cutting-edge technology ensure that every project meets the highest standards of precision, efficiency, and durability.
Experience the benefits of robotic welding first-hand by partnering with Cresco Custom Metals. Contact us today to discuss your manufacturing and engineering needs and take a step towards elevating your operations to new heights of productivity and performance.